Single punch tablet press is also called eccentric press or single station press is the simplest machine for tablet manufacturing. Single punch tablet press, as the name implies employ single set of station tooling that is a die and a pair of upper and lower punches, potable desktop machine.
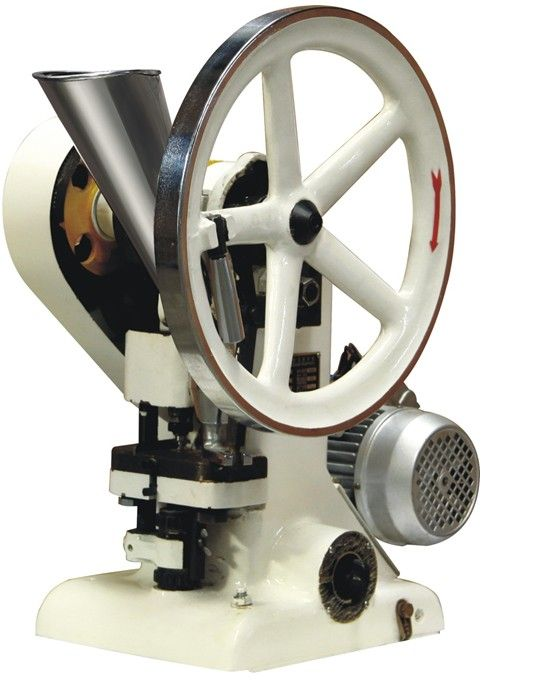
Specification | Peremeters |
Die and punch (set) | 1 |
Max. pressure | 1.5 T |
Max. Dia. of tablet | 12 mm |
Max. Depth. | 11 mm |
Max. depth of tablet | 6 mm |
Throughput | 4000-6000 pcs/h |
Motor power | 370w/380v 550w/220v |
motor speed | 1400r/min |
Dimension | 570×380×630 mm |
Max. Pressure | 15KN |
Weight | 95kg |
Components/ funtional parts of a single punch tablet press
Hopper – This is connected to the feed shoe and it is where the granules/powder mixtures are poured into prior to tableting or compression. The hopper can be filled manually or by using mechanical equipment during subsequent tableting.
Die cavity – The die cavity is where the powder granules are compressed into tablet. The die determines:
The diameter of the tablet
The size of the tablet
To some extent the thickness of the tablet.
check Chart I.
Chart 1 Relationship between sheet weight and flat die diameter
Pill Weight (mg) | Dies Dismater (mm) |
60 | 5.0 |
70 | 5.5 |
70-80 | 6.0 |
100-150 | 7.0 |
200 | 8.0 |
300 | 9.0 |
400 | 10.0 |
500 | 11.0 |
550-650 | 12.0 or 12.5 |
Punches – This comprises upper and lower punch and they compress the powder into tablets of various shapes within the die.
Cam truck – This guides the position/movement of the punches.
Tablet adjuster – This is used to adjust the volume of the powder to be compressed and so determines the weight of the tablet.
Ejection adjuster – This facilities the ejection of the tablet from the die cavity after compression.
Chart 2 Relationship between pill weight and diameter of punching dies for shallow and deep concave shapes
Pill weight (mg) | Dies dismater (mm) |
60-70 | 5.5 |
65-85 | 6.0 |
120-170 | 7.0 |
160-200 | 8.0 |
210-330 | 9.0 |
350-450 | 10.0 |
450-520 | 11.0 |
≥500 | 12.0 |
Precautions:
Tablet shape aesthetic principles: thickness: diameter = 0.2-0.35.
The diameter will vary slightly, and there may be crossovers depending on the density of the material. For example, sometimes 6mm can be used, while 5.5mm will work, too.
Flat punching is generally used for chewable tablets, buccal tablets, etc. The shallow concave tablets can be coated with film, and the deep concave tablets can be coated with sugar or film. When the tablet weight is large (≥500mg), the special-shaped will make the tablet looks smaller, then it is psychologically easy to be accepted by the patient. When measuring the hardness, it is necessary to measure both sides of the long axis of the special-shaped piece.
Protection of the die: If it is not used for a long time, it needs to be uninstalled, be clean and then be stored with No. 32 engine oil. If it is not used for just a short time, hard magnesium or talcum powder can be applied.
If the die is rusted: polishing slightly with fine sandpaper, do not rub too much, otherwise raw powders will be leaked. Then press tablets repeatedly by using magnesium stearate and compressible starch to remove the rust.
The shape, eg, flat, shallow concave or deep concave tablets, may have certain influence on drug release.
In the production of tablets using single punch, the upper punch compresses the powder into tablets while the lower punch ejects the tablet.
The sequence of events involved in the formation of tablet.
The events involved in tablet production can be divided into 3 stages;
Filing
Compression
Ejection
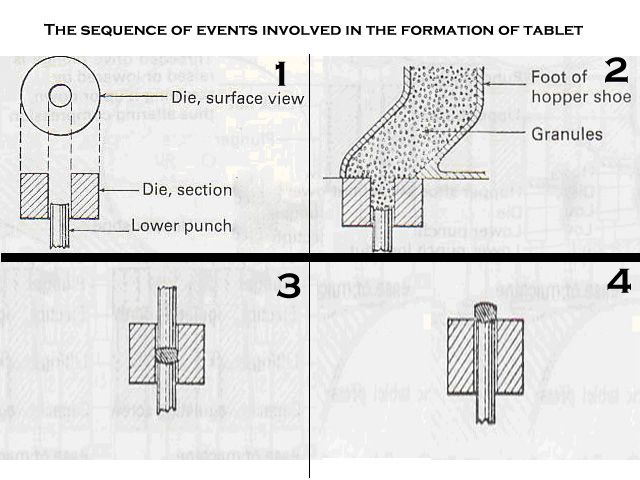
FILING
Position 1 – The upper punch is raised and lower punch drops to create a cavity in the die.
Position 2 – Feed shoe moves over the die cavity and granules fall into the die cavity under the influence of gravity from the hopper.
COMPRESSION
Position 3 – Feed shoe moves out of the way and the hopper punch descends to compress the granules/powder mixture into tablets by progressive reduction of the porosity of the die content and forcing of the particles into close contact with one another.
EJECTION
Position 4 – The upper punch retracts and the lower punch moves upwards too to eject the compressed tablet. The whole events repeat over and over again unit the feed material is exhausted.
Advantages of Single Punch Tablet Press
The single punch structure is rational and small.
Easy to operate and it operates at a high utilization ratio.
It can manufacture odd shaped products with a diameter of up to 20mm.
It is ideal for development of tablets and small batch production.
Single punch tablet press utilizes a high amount of pressure to reduce weight variations between tablets while maintaining a low noise level at the same time.
[Reference]https://www.pharmapproach.com/single-punch-tablet-press/